■孫博
(淄博市特種設(shè)備檢驗(yàn)研究院)
摘要:受到鍋爐壓力容器結(jié)構(gòu)及壓力管道裂紋位置不確定性的制約,管道裂紋檢測精度偏差過大。為了解決這一問題,從
檢測壓力管道結(jié)構(gòu)應(yīng)力與裂紋位置結(jié)構(gòu)應(yīng)力分布特征入手,引入神經(jīng)網(wǎng)絡(luò)處理思路,通過對(duì)鍋爐壓力容器壓力管道裂紋神經(jīng)網(wǎng)絡(luò)有限元分析,獲得待處理信息的神經(jīng)網(wǎng)絡(luò)構(gòu)建關(guān)聯(lián)參量;然后基于神經(jīng)網(wǎng)絡(luò)對(duì)鍋爐壓力容器壓力管道裂紋進(jìn)行應(yīng)力分析,獲得裂紋位置上的應(yīng)力特征及其周邊應(yīng)力差異;接著對(duì)所得參量進(jìn)行裂紋數(shù)據(jù)神經(jīng)網(wǎng)絡(luò)處理,獲得裂紋所在區(qū)域;最后完成壓力容器壓力管道裂紋定位。實(shí)驗(yàn)結(jié)果表明,提出方法切實(shí)有效,并且能夠在最短時(shí)間內(nèi)完成裂紋檢測過程,具有較高的可實(shí)現(xiàn)性,適合大范圍推廣。
0引言
鍋爐壓力容器在石油、化工、冶金等行業(yè)中被廣泛應(yīng)用,在工業(yè)生產(chǎn)中發(fā)揮著重要作用。但由于其結(jié)構(gòu)復(fù)雜、運(yùn)行環(huán)境惡劣[1-2],如果不能及時(shí)發(fā)現(xiàn)存在的安全隱患,容易導(dǎo)致嚴(yán)重的事故。因此,對(duì)鍋爐壓力容器狀態(tài)檢測對(duì)于保障設(shè)備安全運(yùn)行十分重要。
由于鍋爐壓力管道自身結(jié)構(gòu)特點(diǎn),傳統(tǒng)的無損檢測方法存在局限性。例如,利用X射線對(duì)鍋爐壓力管道進(jìn)行檢測時(shí)[3-4],容易受到操作人員主觀因素的影響;而在利用超聲波檢測時(shí)[5-6],由于缺陷的產(chǎn)生時(shí)間和位置具有隨機(jī)性,受外界因素影響較大;利用磁粉檢測時(shí),缺陷的分布通常呈非均勻狀態(tài)[7-8],并且檢測面較小、干擾因素多、難以定量等。受上述諸多因素的影響,造成壓力管道檢測方法整體檢測誤差偏大,亟需一種檢測方法解決上述問題。隨著人們對(duì)神經(jīng)網(wǎng)絡(luò)研究的深入,發(fā)現(xiàn)神經(jīng)網(wǎng)絡(luò)可以有效解決壓力容器壓力管道裂紋檢測過程中擾動(dòng)因素的分離問題,進(jìn)而提升裂紋檢測精準(zhǔn)度,基于此特點(diǎn),研究基于神經(jīng)網(wǎng)絡(luò)的鍋爐壓力容器壓力管道裂紋檢測方法。
1方法的具體實(shí)現(xiàn)
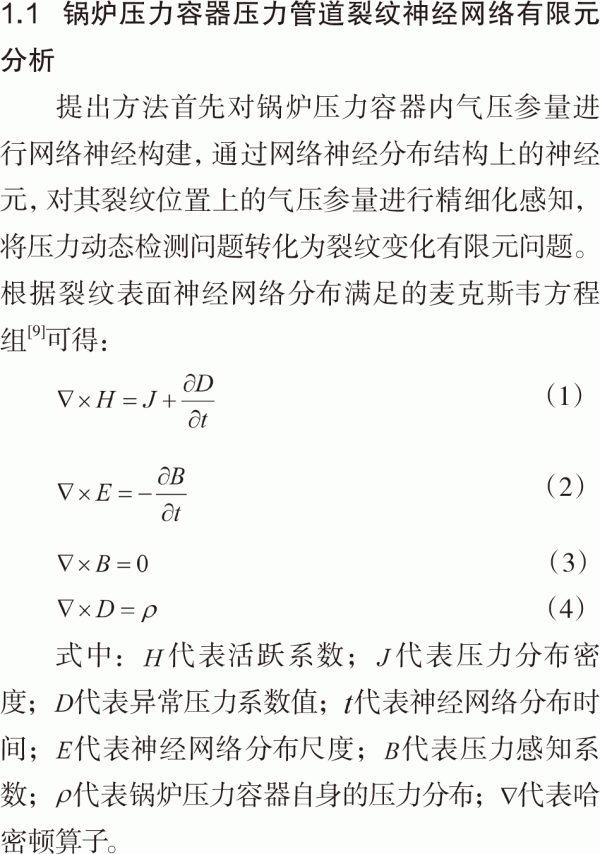
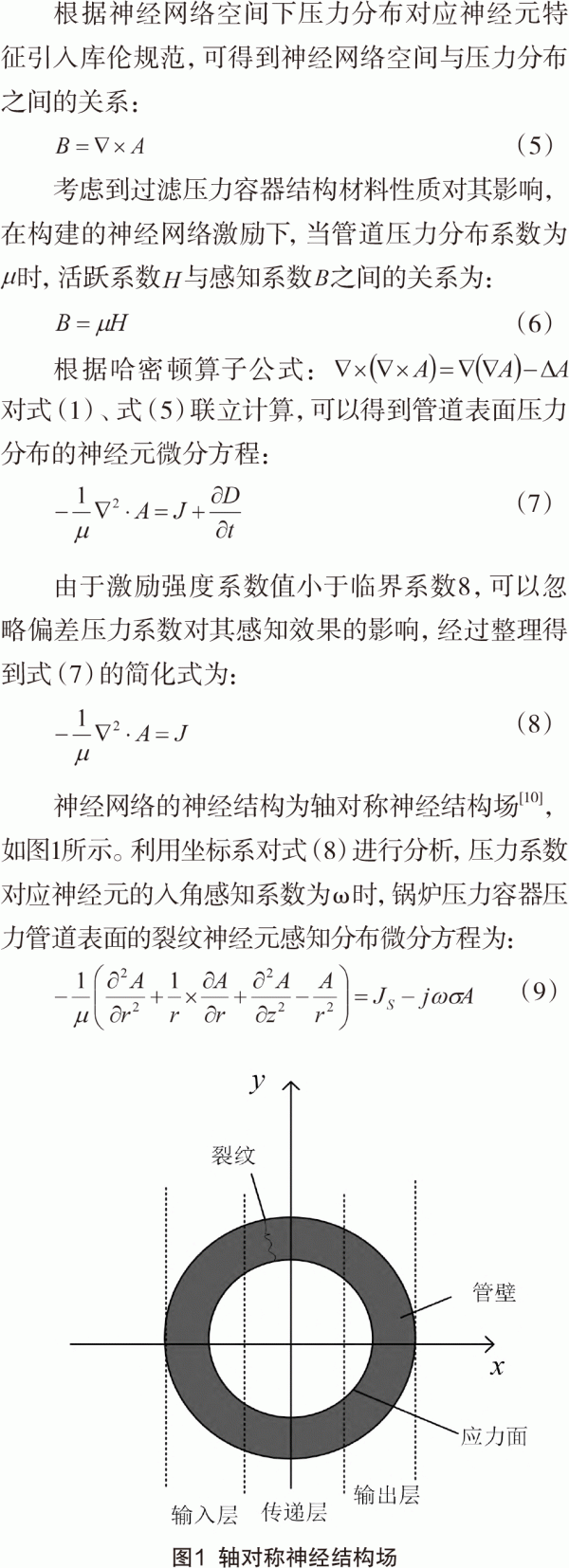
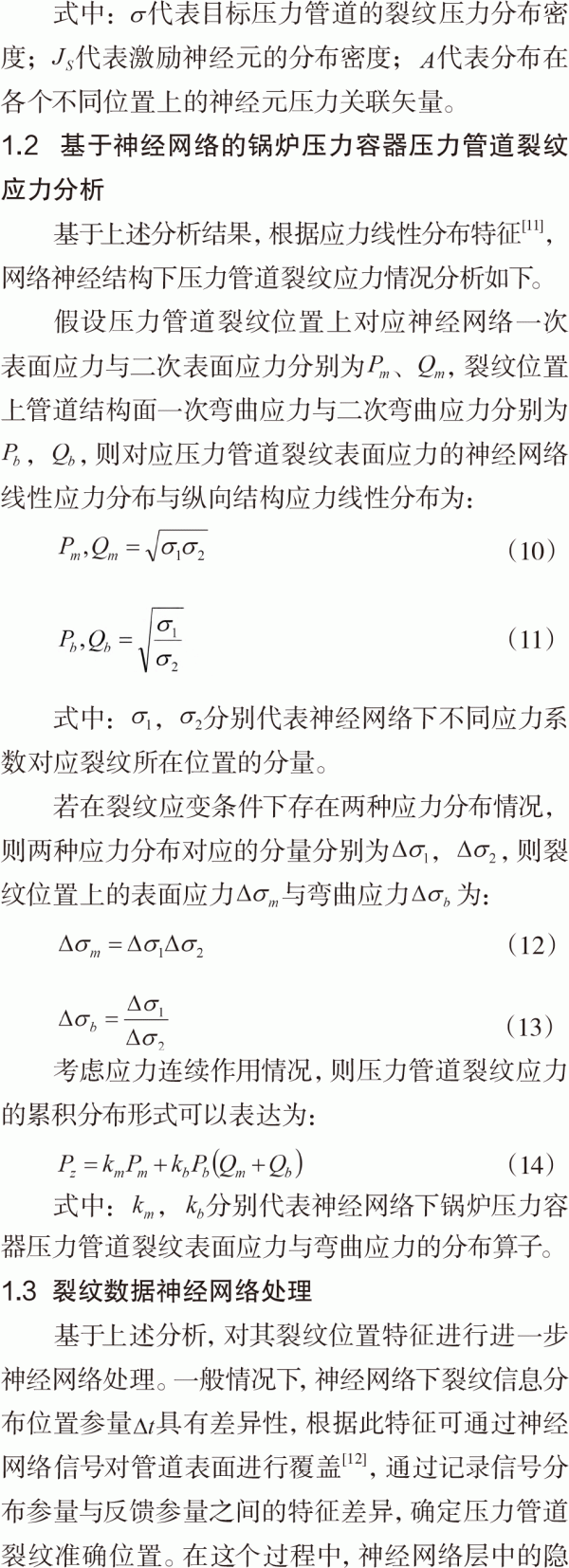
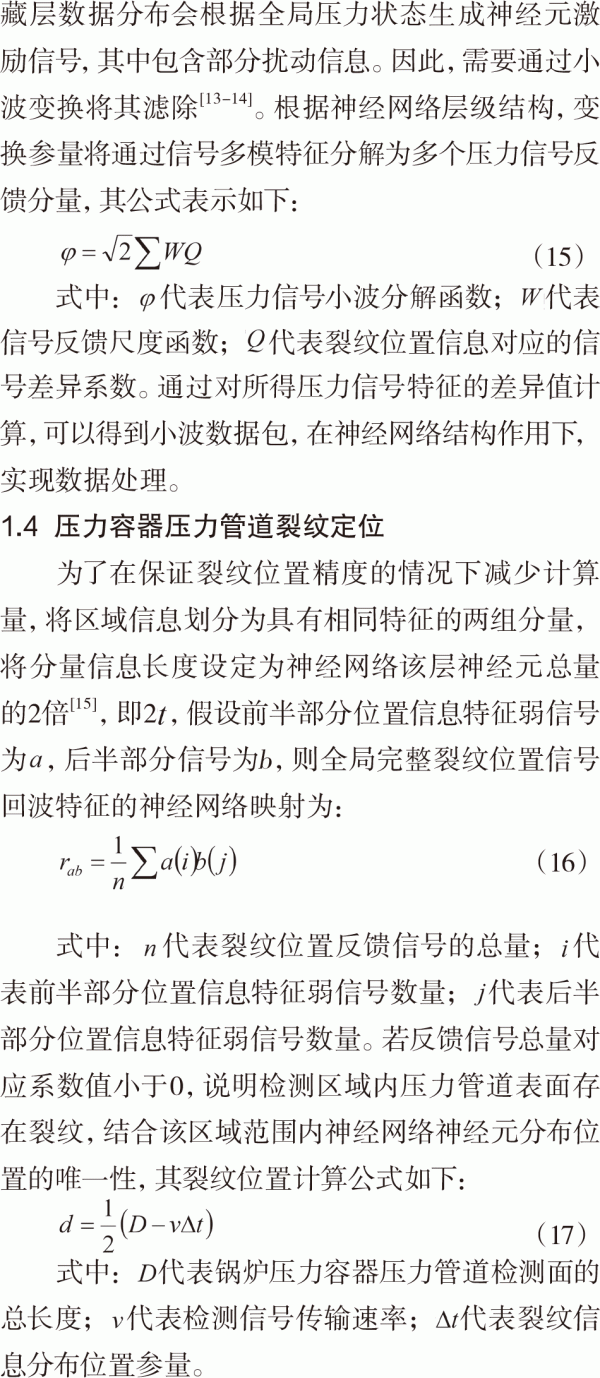
2應(yīng)用測試
對(duì)提出檢測方法進(jìn)行實(shí)例數(shù)據(jù)的測試,通過實(shí)例數(shù)據(jù)構(gòu)建測試場景,在搭建的場景中,與引入的3種不同檢測方法的性能對(duì)比。其中引入的3種檢測方法作為參照方法參與測試,分別基于平衡電磁的壓力管道檢測方法,標(biāo)記為參照方法A;基于圖像邊緣特征的壓力管道裂紋檢測方法,標(biāo)記為參照方法B;基于圖像差異特征的管道裂紋識(shí)別方法,標(biāo)記為參照方法C;提出方法標(biāo)記為驗(yàn)證方法。根據(jù)實(shí)例數(shù)據(jù)配置及測試要求動(dòng)態(tài)生成測試樣本,完成相關(guān)指標(biāo)數(shù)據(jù)量的測試、對(duì)比、分析,并得出解釋結(jié)論。
2.1設(shè)置測試條件
測試數(shù)據(jù)采用某一供熱企業(yè)鍋爐數(shù)據(jù)作為基礎(chǔ)數(shù)據(jù),其中用于測試數(shù)據(jù)采集傳感器偏差參量根據(jù)鍋爐管道內(nèi)介質(zhì)溫度不同有所不同,具體參量如表1所示。另外,管道內(nèi)介質(zhì)渦流對(duì)裂紋壓力的動(dòng)態(tài)影響系數(shù),如表2所示。
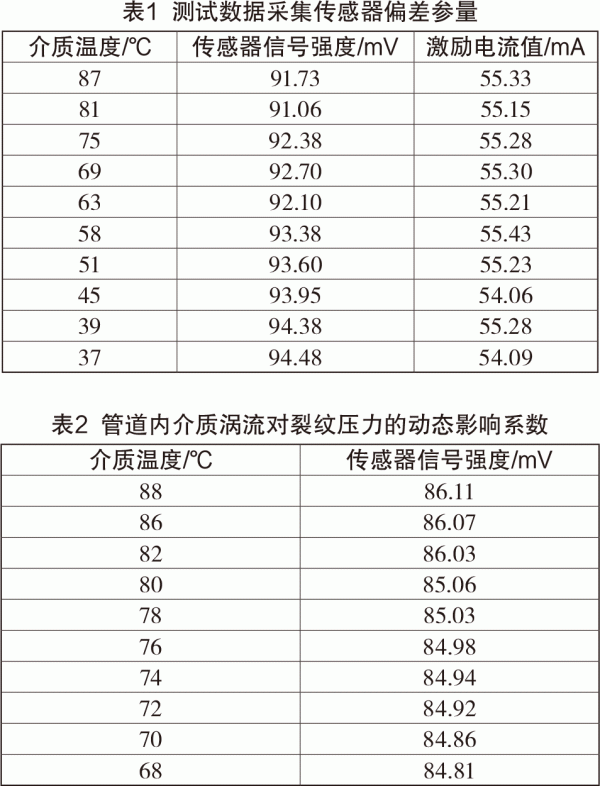
2.2裂紋檢測誤差測試
根據(jù)上述設(shè)定的測試參量,由測試工具隨機(jī)生成一組壓力管道裂紋數(shù)據(jù),并由四種方法對(duì)其進(jìn)行裂紋檢測,檢測結(jié)果分別對(duì)應(yīng)圖2-5。
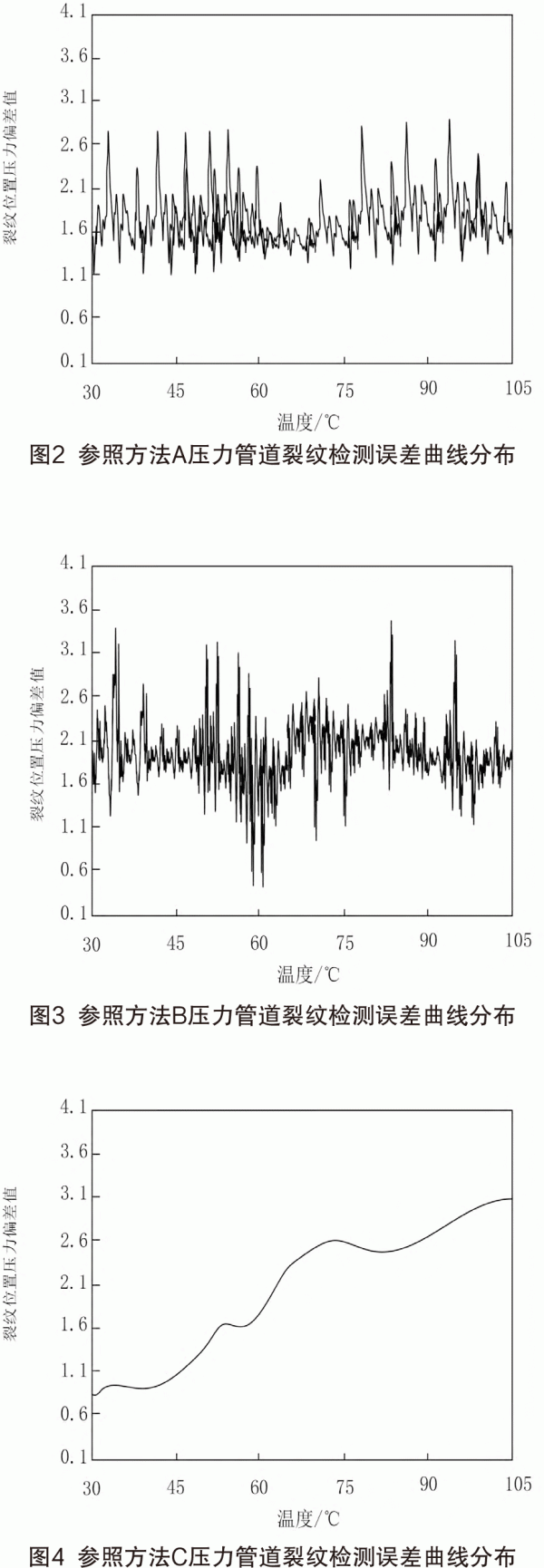
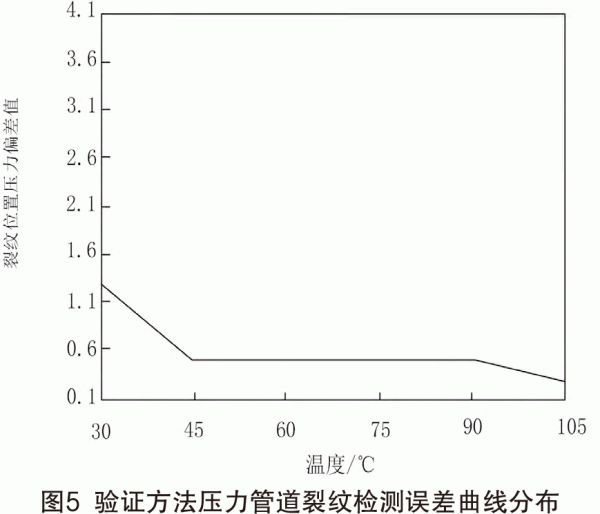
通過觀察對(duì)比發(fā)現(xiàn),參照方法A與參照方法B所得曲線特征相似度較高,說明兩種檢測方法在裂紋感知層面屬于同一屬性。因此分析兩種檢測方法測試結(jié)果,經(jīng)過觀察指標(biāo)變化發(fā)現(xiàn),參照方法B的波動(dòng)頻率大于參照方法A,說明裂紋識(shí)別過程中存在大量擾動(dòng)信息,從數(shù)值分布上看,兩種檢測方法的效果十分相近,參照方法A略好于參照方法B;與圖2圖3不同,圖4與圖5可以明顯看出兩種方法的檢測屬相具有線性特征,其區(qū)別在于圖4曲線對(duì)應(yīng)的參照方法C屬于遞增曲線,其過程中可以看到擾動(dòng)因素;因此對(duì)應(yīng)誤差值隨著管道溫度上升,壓力不斷增大,相應(yīng)裂紋位置上的結(jié)構(gòu)應(yīng)力隨之增大,在擾動(dòng)因素作用下檢測可信度降低,誤差不斷增大;與之相反,圖5中曲線屬于遞減線性特征,且看不到擾動(dòng)因素,說明該方法所得參量經(jīng)過濾波處理,因此所得參量的可信度較高,誤差值隨溫度的增長,會(huì)達(dá)到臨界值,從而所得參量將一直保持最優(yōu)值狀態(tài),直至壓力管道溫度打破管道裂紋位置能夠承受的峰值溫度。綜上所述,根據(jù)測試所得誤差值由小到大排列,參測方法的檢測性能排序?yàn)轵?yàn)證方法、參照方法C、參照方法A、參照方法B。
2.3檢測方法可信度測試
按照上述測試樣本參量配置標(biāo)準(zhǔn),循環(huán)釋放40組相同數(shù)據(jù),重復(fù)時(shí)間間隔為15s,獲得40組測試誤差統(tǒng)計(jì)數(shù)據(jù),每兩組誤差數(shù)據(jù)作為1組進(jìn)行差值對(duì)比,誤差值為0,標(biāo)記為√;誤差值不為0,標(biāo)記為×;以此獲得20組可信度統(tǒng)計(jì)表,如表3所示。最后統(tǒng)計(jì)√數(shù)量,數(shù)量越多,說明可信度越高。
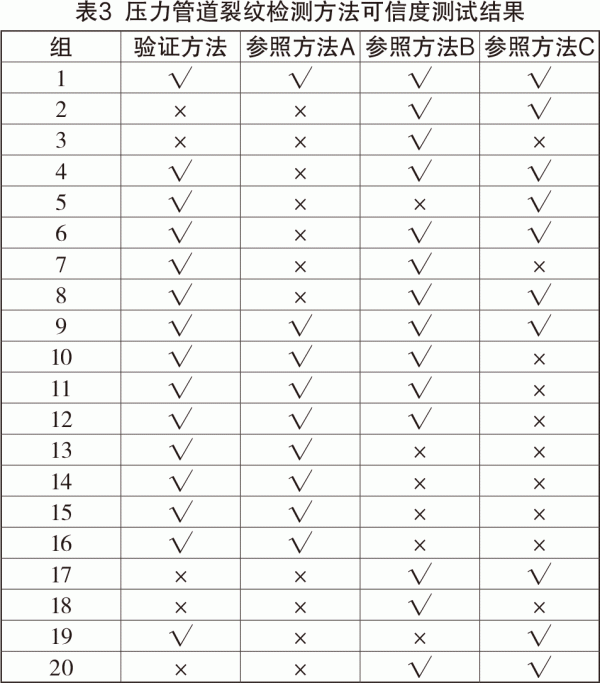
根據(jù)表3所示的數(shù)據(jù)來看,驗(yàn)證方法√標(biāo)記總數(shù)為15組;參照方法A√標(biāo)記總數(shù)為9組;參照方法B√標(biāo)記總數(shù)為14組;參照方法C√標(biāo)記總數(shù)為10組。經(jīng)過統(tǒng)計(jì)參與測試的4種壓力管道裂紋檢測方法的可信度排序按照由高到低的順序?yàn)椋候?yàn)證方法、參照方法B、參照方法C、參照方法A。
3結(jié)語
基于鍋爐壓力容器壓力管道應(yīng)力分布特征對(duì)裂紋的影響,引入神經(jīng)網(wǎng)絡(luò)算法對(duì)其裂紋位置應(yīng)力及其相關(guān)參量進(jìn)行神經(jīng)網(wǎng)絡(luò)構(gòu)建,在神經(jīng)網(wǎng)絡(luò)空間下完成裂紋位置檢測準(zhǔn)確性的優(yōu)化。提出檢測方法雖然能夠解決現(xiàn)階段鍋爐高壓容器高壓管道裂紋檢測誤差大的問題。但是,從方法識(shí)別范圍及其約束寬容度角度來說,該方法并不完善。這是因?yàn)樯窠?jīng)網(wǎng)絡(luò)中每一個(gè)神經(jīng)元均受到自身生命周期的限制,導(dǎo)致對(duì)應(yīng)局部神經(jīng)網(wǎng)絡(luò)對(duì)裂紋位置上應(yīng)力變化的感知靈敏度降低,進(jìn)而存在二次誤差風(fēng)險(xiǎn)。為了避免這一問題的發(fā)生,在未來的研究中,可以基于壓力管道材質(zhì)特征,引入電磁信號(hào)作為神經(jīng)網(wǎng)絡(luò)數(shù)據(jù)載體,進(jìn)而減輕對(duì)神經(jīng)網(wǎng)絡(luò)的依賴程度,提升裂紋數(shù)據(jù)精準(zhǔn)度,完善檢測方法。
參考文獻(xiàn)
[1]趙建政,宋偉斌.基于小波域的鍋爐壓力容器壓力管道裂紋X射線檢測方法[J].自動(dòng)化與儀表,2023,38(1):86-89,104.
[2]強(qiáng)敏娜,張良,王永樂,等.在用壓力管道裂紋檢驗(yàn)中無損檢測技術(shù)分析[J].山西化工,2023,43(1):160-161+166.
[3]姚俊峰.鍋爐和壓力容器及壓力管道檢驗(yàn)中裂紋問題探討[J].設(shè)備管理與維修,2023(2):94-95.
[4]王明庭.壓力管道施工監(jiān)檢常見問題分析及改進(jìn)措施[J].中國特種設(shè)備安全,2022,38(12):58-62.
[5]王沖,王彥軍,周順,等.基于有限元研究某站場天然氣壓力管道應(yīng)力分析及缺陷評(píng)估[J].當(dāng)代化工研究,2022(24):116-118.
[6]林寅.某食品車間蒸汽鍋爐壓力管道開裂原因分析[J].化工裝備技術(shù),2022,43(6):13-15.
[7]林三福.管道焊口熔銅裂紋PAUT檢測圖譜特性和磨開驗(yàn)證分析[J].運(yùn)輸經(jīng)理世界,2022(34):152-154.
[8]高聰.鍋爐壓力容器壓力管道檢驗(yàn)中的裂紋問題分析[J].中國設(shè)備工程,2022(19):158-160.
[9]鄭于賢.鍋爐壓力容器壓力管道檢驗(yàn)中的裂紋問題[J].化學(xué)工程與裝備,2022(9):270+269.
[10]王長新,陳金忠,辛佳興,等.基于SSA-BP神經(jīng)網(wǎng)絡(luò)的管道裂紋渦流識(shí)別研究[J].石油機(jī)械,2022,50(8):118-125.
[11]郭素琴.鍋爐壓力容器壓力管道檢驗(yàn)中的裂紋問題研究[J].中國新技術(shù)新產(chǎn)品,2022(14):79-81.
[12]冉蓉,徐興華,邱少華,等.基于深度卷積神經(jīng)網(wǎng)絡(luò)的裂紋檢測方法綜述[J].計(jì)算機(jī)工程與應(yīng)用,2021,57(9):23-35.
[13]蔡勤,李繼承,戚政武,等.基于脈沖渦流(瞬變電磁)技術(shù)的帶包覆層壓力管道壁厚檢測研究[J].熱加工工藝,2023,52(2):21-26.
[14]關(guān)靜,樓飛.基于邊緣輪廓的管道裂紋缺陷檢測算法研究[J].計(jì)算機(jī)與數(shù)字工程,2022,50(5):1103-1108.
[15]蘇林,馬雪莉,崔德榮,等.基于周向勵(lì)磁的管道缺陷漏磁信號(hào)仿真分析[J].電焊機(jī),2022,52(3):20-28.
|