黃彬
(江西省檢驗檢測認證總院特種設備檢驗檢測研究院宜春檢測分院,江西宜春336000)
摘要:由于工作人員對鍋爐使用過程中存在的一些安全問題重視程度不高,壓力管道經常會出現裂紋,從而大幅降低鍋爐質量,增大設備安全運行風險。為強化安全生產、促進行業的發展,對鍋爐壓力容器的壓力管道裂紋問題進行深入研究,并針對一些常見裂紋提出有效的維修保護措施,提高工作效率。
0引言
目前鍋爐壓力容器已經成為現代工業中最常用的一種設備,在冶金、機械、電力、石化等行業的應用日益受到人們關注。從生產工藝來看,為達到節能的目的,現在鍋爐壓力容器主要是以大型設備為主,結構更加復雜。在運行過程中鍋爐壓力容器會發生不同程度的結構破壞,從而引起壓力管道內的裂紋,對整個容器的質量造成較大影響,成為管道破裂的安全隱患。腐蝕孔隙的壓力也會使管道產生裂紋。
隨著社會經濟的發展,電站鍋爐技術逐步發展,壓力管道是火電站鍋爐的主要承壓設備,其參數變化也在逐漸增加,因此火電站對管道質量要求也在逐漸提高。近年來,電站發生了大量壓力管爆裂和故障,并逐步引起業界對其質量監管的重視。在壓力管道中,合金高壓鍋爐管(12Cr1MoVg)是一種廣泛應用的耐熱管材,關于其焊接性能與材料性能已經進行了大量研究,相關理論日趨完善,然而由于電站的施工現場環境十分復雜,合金高壓鍋爐管的施工很難獲得理想效果。本文將以某火電站鍋爐的壓力管道為例,對裂紋的產生展開分析與處理。
1裂紋理論——應力強度系數
在裂紋理論中,應力強度系數是根據裂紋尺寸確定的。裂紋產生的主要原因是應力強度系數增大,而臨界應力強度系數可以反映材料的裂紋性能,因此理論上可以將其定義為裂紋韌性。針對應力腐蝕裂紋而言,由于鍋爐內鋼板與高濃度介質的接觸,導致其晶間和金屬晶體之間的電勢差異,從而導致高的晶粒電勢成為陰極;而作為陽極的晶間,會在晶粒與晶間形成微小的電流,不斷侵蝕鍋爐的結構,使其內部結構產生裂紋。
裂紋是由內部向外部擴散的苛性脆性因子引起的,并最終集中于應力最大的位置,從而導致該區域出現裂紋。由于裂紋產生的時間很短,而且會隨著鍋爐之間的晶體結構而發生改變,在微電流的作用下裂紋面積會逐漸增大,加重裂紋的問題。
裂紋理論定義了由裂紋引起的裂紋現象,即裂紋尖端的應力強度系數K,大于或超過裂紋材料的裂紋韌度K,這意味著裂紋已經進入了一種不穩定的狀態,會穿過結晶、沿著結晶結構繼續發展。最后,顯微鏡下如果出現一種輻射狀裂紋,則是由鍋爐內部的裂紋引起的,隨著裂紋的擴大裂紋形狀也會發生改變,從而導致整個結構的裂紋。
2壓力容器和壓力管道檢驗內容和方法
根據現行國家標準,對鍋爐壓力容器、管道等檢驗方法主要分為3類,通過它們能夠使其符合規定的使用要求。這3種檢查方式為內部檢查、外部檢查和水壓檢查,測試必須遵循一定的程序。在正式測試前,首先要對各類儀器的外觀、安全監控系統的運行情況進行檢查,在保證所有員工都具備相應的資格后,隨后是對所有設備和管道進行全方位檢查。無論是內部檢查還是外部檢查、水壓試驗,都要按照技術規范和規范進行。
在完成檢測后,通常需要對實際使用環境進行預試驗,以判斷該裝置能否正常工作;對設備進行檢查,確認無任何問題,方可投入使用。同時,要重視易產生裂紋的部位的檢查工作,定期對其進行安全、完整性的檢驗,發現問題的要及時進行處理。
3壓力容器壓力管道常見的裂紋
在鍋爐壓力容器的管道檢查中,大多數裂紋表現為表面裂紋,其尺寸遠小于其本身的彎曲半徑。對于裂紋問題的分析,可以把裂紋等效為帶有半橢圓形裂紋的板受拉問題(表1)。某鍋爐壓力容器的軸向應力為83.2MPa,環向應力為146MPa。根據應用力學的原理,在鍋爐壓力容器的壓力管道中內部壓力將會產生最大主應力σ1和環向應力σ2。
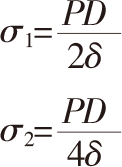
其中,P是指鍋爐內壓容器的內部壓力,D、δ表示壓力容器的內徑和壁厚。從應力公式可以看出,在容器壓力管道中,環向應力是最大的主應力,將其應用于裂紋端應力強度系數的計算,并將其與相應的計算模式相結合[1]。
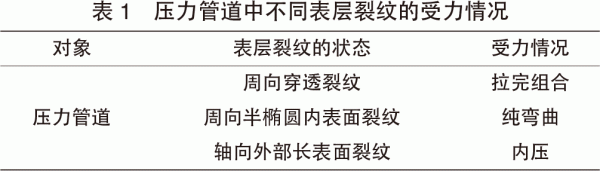
3.1疲勞裂紋
在長期使用中,某些壓力容器、壓力管道會因交流負載而產生裂紋,如蒸壓釜、滅菌鍋、壓力管道的膨脹節等,在運轉時會由于受力不均極易產生裂紋。在許多壓力管道難免會產生一些裂紋,稱為疲勞裂紋。所以,有關主管部門應根據管道的質量和工作環境,對管道進行定期的檢查和維修,以及時發現問題。在檢修和維護此類管道時,應重點關注應力集中的位置。這種疲勞裂紋的產生通常與設計工藝、材料、焊接工藝密切相關,可以通過改進工藝流程、合理選用材料,改進現有的不合理之處。其中每一步都是相輔相成、相互影響的,任何一個環節出現問題都會影響制造和生產,從而造成疲勞裂紋。
根據工作實踐判斷疲勞裂紋的不同成因,將其劃分為機械疲勞裂紋和腐蝕裂紋:機械疲勞裂紋是由管道的各個部位應力分布不均引起的,初期裂紋很小,但在持續的加壓下裂紋不斷擴大(圖1);腐蝕破壞是因為管道中含有腐蝕性的物質,在壓力的作用下出現裂紋(這種腐蝕裂紋會逐漸發展成機械疲勞裂紋)并有逐漸擴大的趨勢,其在設備使用中會逐漸加長,從而對管道的壽命造成較大影響。無論是哪種疲勞裂紋,都應及早發現、及早處置,以免裂紋逐漸增大、影響設備的正常使用。
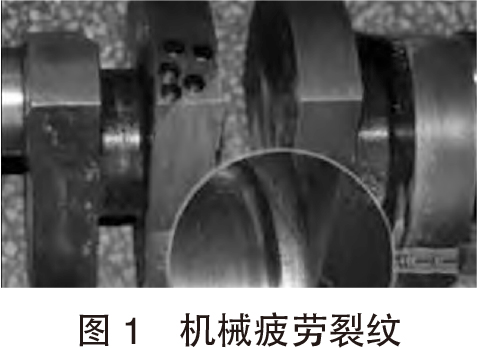
3.2蠕變裂紋
隨著現代機械制造水平的提高,對各種工藝技術的要求越來越高,對壓力容器、壓力管道的設計也越來越嚴格。長時間處于高溫、高壓的環境中,很容易產生蠕變裂紋,特別是某些金屬材料的壓力容器、管道,在高溫、高壓的作用下會產生裂紋(圖2)。這直接關系到設備的正常使用,所以應對進行全面檢查,找出存在的安全隱患,防止因裂紋而影響設備的正常工作。
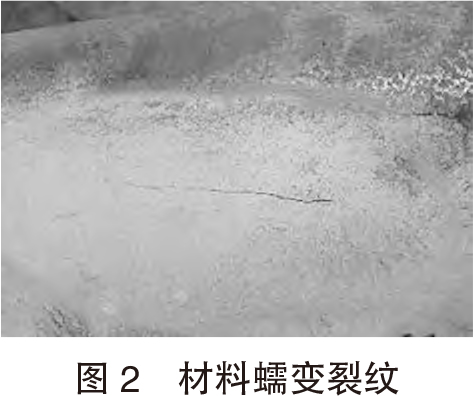
一般認為蠕變裂紋的形成可以分成3個階段:從穩定蠕變期到加速蠕變,再到加速蠕變,初期的蠕變,這個階段非常隱蔽;其產生與環境壓力、溫度、時間等因素密切相關,許多因素都會對其產生影響,應及早發現、及早處置,確保設備安全、穩定。
4檢驗合金高壓鍋爐管的對接焊縫裂紋
在本電站中,1號鍋爐過熱器具蒸汽出口壓力為18MPa,過熱蒸汽溫度為539℃,最后級的過熱器有兩個三通,位于爐右側和爐左側。出水頭的左、右兩個出水頭通過連通管與最后級的過熱水頭相連。連接管和三通均采用高強度合金燒成鋼管,連接管尺寸為650mm×85mm。對最終過熱器左側三通與連接管道的對接焊接接頭進行磁粉檢測,發現3條縱向焊接裂縫,它們貫穿整個焊接接頭,并逐步向熱影響區延伸。通過焊接接頭,超聲波探頭的中心線,對焊縫的兩邊進行平行掃描,發現有一道裂縫,深度為54mm。僅查看裂紋的外部,裂紋表面是不連續的、開口較大,并且末端較圓。然后,用切割器對其進行切割,發現這道橫切的裂痕深57mm、長61mm,如同焊縫中有刀片插入。
為提高檢測缺陷率,首先修整焊接余高,然后用超聲波再次檢測及磁粉檢測,在焊接接頭的表面上發現了許多橫斷面上密布裂縫。這么多的裂縫,僅憑超聲波根本無法確定它們到底有多深,因此應一層層地將裂紋進行橫磨,每磨到30mm的深度就做一次磁性檢測。每一層中均有較細的裂隙,但裂隙并非完全連續,且在分布上有不同程度的差別。
5分析合金高壓鍋爐管的對接焊縫裂紋
高強度合金鍋爐鋼管是一種具有珍珠巖結構的耐熱鋼種,一般在700~750℃高溫回火、再在980~1020℃正火來供應。通過對電站現場進行無損檢測試驗,找出產生裂紋的主要原因。
5.1管道外表面微波無損檢測
本文提出一種基于點頻和掃頻的方法,利用具有開放末端的矩形波導管做檢測器,對金屬表面進行掃描。裂縫的出現會導致高階模態出現,進而影響已經在波導中形成的微波性質。
所設計的掃頻法微波檢測裝置如圖3所示,采用非破壞式線纜,將微波反射電橋的一端與微波向量網絡分析器的輸出端、輸入端相連,而電橋的另一端與波導探針相連,在測量過程中對波導探針的開口與被測量的金屬表面垂直進行掃描,測量結果與實際一致。
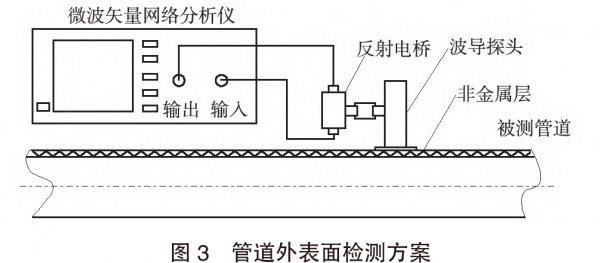
在微波矢量網絡分析裝置中,通過微波信號源饋入電橋,通過波導探測器輸出與待測物質發生作用,物質的電磁性質會改變待測物質的空間分布狀態,進而改變待測物質的幅值、相位等基礎參數,通過反射電橋將待測物質反射、反饋到裝置中,從而實現對待測物質的掃描。
最后,將通過網絡分析儀觀測到的特性參數輸入計算機,對數據進行分析和統計,進而對被檢測物質的缺陷狀況和其他物理參數做出判斷。
5.2管道內表面微波無損檢測
將被測金屬管當作是一種波導,利用矢量網絡分析器法測量管子的透射與反射性能,判定與定位管子的缺陷。波導中微波的傳輸特性主要由3個因素決定:一是微波的特征參量,如頻率、模式等;二是波導的特征參量,如波導斷面的形態和大小參量等;第三個是被填入波導內的物質的特征參量,如媒質的導電系數等。其中,任何一個參數的改變都會引起波導中電磁波傳輸性質的改變。在試驗探測過程中,可以在管壁上預加特定尺寸的裂紋等缺陷,從而改變波導的特征參量,影響管壁的電磁環境,造成其他模式在管壁的傳播,從而對管壁的電磁波產生反射與散射,影響管壁電磁波的傳播。在此基礎之上,對不同形狀、不同尺度試樣的類型等進行測試。

管道的內表面檢測方案如圖4所示:將電橋兩端連接到微波向量網絡分析儀的輸入端,而電橋則連接到波導同軸變換器,并在被測管與波導同軸變換器之間連接矩—圓波導,實現TE10-TE11模態的變換。管道的末端在開口期間為開路狀態,封閉時為短路狀態,在兩種狀態下均可檢測管道內壁缺陷。
6處理合金高壓鍋爐管的對接焊縫裂紋
從上面的分析可以看出,該對接焊縫裂紋數量、深度、長度較為特殊,在進行了多方考量之后,最終決定采用環切坡口機徹底清除焊縫缺陷。
首先切一個深61mm、寬13mm的切口,利用坡口刀將上下的坡口推出,再利用圓角刀切掉槽底上下的圓角,檢查完畢、確認合格后,利用坡口刀將圓角、修切坡口平滑過渡,變成一個U形的坡口。根據上述對高溫合金鍋爐管裂紋成因的分析,應使用不含有任何雜質的Ti作為焊縫物質,而且這種物質必須符合光譜的要求,即焊接前必須采用電加熱的方式進行預熱,在200~300℃進行焊接。
實施焊接作業時,必須使層與層之間的溫度保持在200~400℃。單層焊縫的厚度比電極直徑長2mm,但軌的旋轉寬度比電極直徑小5倍。焊接時,要注意每一層的焊接并注意收弧、起弧的焊接質量。由于是對集箱三通和連通管進行焊接,因此要有適當的溫度補償,合理、科學布置加熱器,在焊縫的中央要對稱布置,兩側均要超過4個,以確保焊縫的溫度準確、可靠。室溫下在任何一個受熱區域內,兩個測量點的溫度差不得超過50℃。另外,應采用合適的焊接方式,最大限度提高焊接質量。
修復工作結束后,對焊接接頭進行各項試驗,未發現任何缺陷,而且焊縫為回火貝氏體組織,硬度也很高,這表明裂紋得到了有效控制。
7結束語
在正常使用時鍋爐、壓力容器和壓力管道不允許發生裂紋問題,裂紋是由內部和外部兩方面因素共同作用而形成的,會對設備和管道的正常使用造成較大影響。為了提高鍋爐、壓力容器、壓力管道的使用安全性,必須嚴格對設備進行檢查和維修,合理運用現行的檢測技術,以最低的成本發現裂紋,并采用相應的防治措施保障鍋爐、壓力容器及壓力管道的安全、平穩運行。
參考文獻
[1]高聰.鍋爐壓力容器壓力管道檢驗中的裂紋問題分析[J].中國設備工程,2022(19):158-160.
[2]鄭于賢.鍋爐壓力容器壓力管道檢驗中的裂紋問題[J].化學工程與裝備,2022(9):270,269.
[3]郭素琴.鍋爐壓力容器壓力管道檢驗中的裂紋問題研究[J].中國新技術新產品,2022(14):79-81.
[4]錢冰,張樹川,姚新寬.鍋爐和壓力容器及壓力管道檢驗中裂紋問題分析[J].新型工業化,2022,12(7):67-70.
[5]萬鵬.壓力容器壓力管道檢驗中裂紋問題的解決措施[J].新疆有色金屬,2022(3):30-31. |