周天1,趙葉靜1,劉志強1,李國選2,崔培哲2,楊聲1
(1.中南大學能源科學與工程學院,湖南長沙,410083;2.青島科技大學化工學院,山東青島,266042)
摘要:為探究傳統制氫工藝與新型制氫工藝的經濟性與環保性,采用技術經濟分析和生命周期評價(LCA)的方法對煤制氫過程和生物質制氫過程產生的溫室氣體(GHG)排放和能源消耗(EC)進行分析,其中,技術經濟分析包括總資本投資(TCI)和生產成本,系統生命周期邊界包括原料生產與運輸、合成氣體的產生、氫凈化、氫的運輸和應用。研究結果表明:與煤制氫工藝相比,生物質制氫工藝的原料消耗和總資本投資大,但生產成本低,排放的溫室氣體少;生物質制氫工藝的能耗與煤制氫工藝的能耗相比低75.4%,溫室氣體排放量比煤制氫過程的排放量低89.6%。
氫作為一種重要的多功能清潔能源載體,在減少溫室氣體排放、維護能源安全、保護環境等方面受到了全世界的關注[1],發展前景廣闊。目前,許多研究和能源政策都集中在氫經濟方面,而氫氣生產是其中重要的一環。中國傳統化石燃料制氫技術主要包括煤制氫和天然氣重整制氫[2]。隨著化石燃料逐漸減少,社會對溫室效應的關注度不斷提升,可再生能源制氫能夠減輕環境壓力[3],因此,發展潛力巨大,其中生物質以其綠色、低碳、清潔、可再生的特點受到了廣泛關注。目前,煤制氫與生物質制氫是氫能工業發展的重要主題[4−8]。與煤制氫相比,生物質制氫雖然降低了化石燃料的使用,但是生產成本高,氫氣生產率低,因此,需要進行經濟技術綜合分析對這2種制氫方式進行比較。而生命周期評價(LCA)[9−11]能對成本效益、能源消耗和環境影響進行系統分析,是一種評價系統環境影響的有力方法,目前已經應用于煤制氫和生物質制氫進程[12]。COHCE等[13]在灰熔聚流化床氣化的基礎上分析了煤制氫過程的生命周期,發現采用碳捕集與儲存技術(CCS)的煤制氫能耗比不采用CCS的煤制氫能耗高2.32%,而溫室氣體排放低81.72%。VERMA等[14]開發了1個LCA模型,用于估算有/無碳捕獲和存儲的地下煤炭氣化(UCG)生產氫氣過程中的溫室氣體排放,發現采用UCG-CCS技術制氫的生命周期溫室氣體排放比蒸汽甲烷重整(SMR)系統的低。程婉靜等[15]采用生命周期成本分析,以煤制氫為起點,結合不同儲運方式和加氫站應用分析了煤氣化和煤熱解這2種技術下煤制氫產業鏈的生命周期經濟性水平。KALINCI等[16]通過生命周期評價比較了生物制氫系統中下吸式氣化爐(DG)和循環流化床氣化爐(CFBG)的化石能源消耗率和溫室氣體排放量等性能,發現DG溫室氣體減排成本為0.0172$/g,而CFB系統為0.24$/g。目前關于煤制氫和生物質制氫工藝能源消耗和環境影響方面的綜合評價與定量分析較少,為此,本文作者針對生物質制氫過程和煤制氫過程進行流程模擬,從總投資成本和生產成本角度對其技術經濟效益進行分析和比較,從能源消耗和溫室氣體排放方面對其生命周期進行分析。
1流程模擬
由于中國秸稈產量十分豐富,且相較于其他能源價格低廉,因此,本文選用秸稈作為生物量進行工業分析和元素分析[17],結果見表1[10,18−19]。基于Aspen Plus模擬生物質制氫和煤制氫過程,得出不同原料制氫工藝流程圖分別如圖1和圖2所示。生物質制氫過程單元主要包括生物質預處理單元(BPU)、空分單元(ASU)、氣化單元(GU)、水煤氣變換單元(WGSU)、低溫甲醇洗單元(RU)、克勞斯單元(CU)、變壓吸附單元(PSAU)、燃氣和蒸汽渦輪發電單元(GSTU)。其主要工藝流程為:氣化劑(氧氣、蒸汽)與生物質原料通過生物質預處理單元處理后送到生物質氣化裝置中進行生物質氣化反應,并生成原料合成氣,此時,合成氣中仍含有焦油、氨氣、苯酚等雜質,利用水蒸氣將雜質洗去后送入水煤氣變換單元。水煤氣變換氣通常包含酸性氣體以及大量的雜質,需要進一步純化。經過純化后的合成氣被送入變壓吸附裝置中進行氣體分離。與此同時,可以利用酸氣脫除裝置將分離出的H2S氣體回收以生產硫磺。
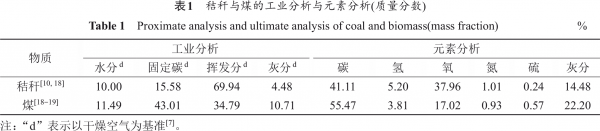
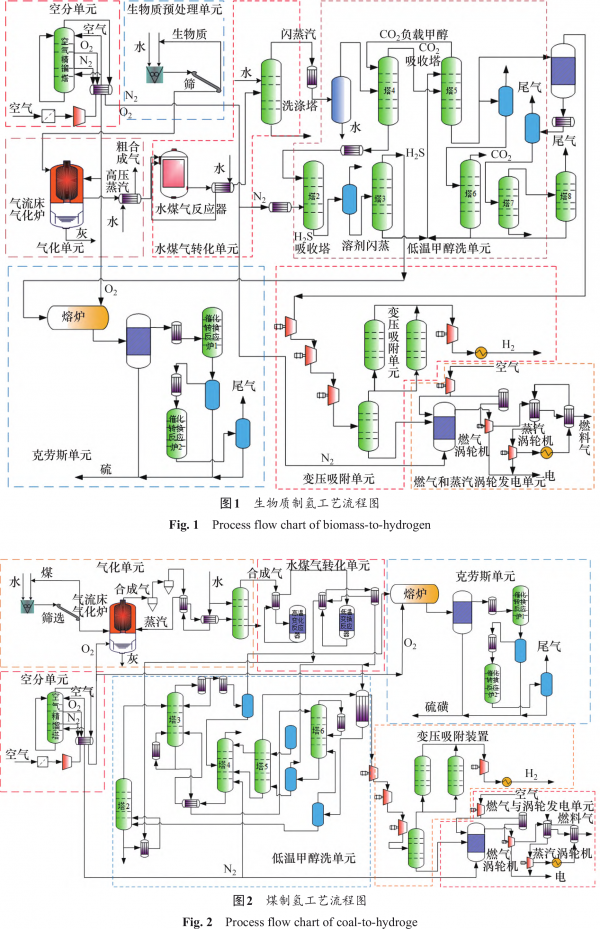
同樣地,煤制氫過程主要由7個單元即空分單元(ASU)、氣化單元(GU)、水煤氣變換單元(WGSU)、低溫甲醇洗單元(RU)、克勞斯單元(CU)、變壓吸附單元(PSAU)、燃氣和蒸汽渦輪機單元(GSTU)組成。種制氫工藝各單元的關鍵模型及性能方法見表2[20−23],工藝規范見表3[20−23],各單元工藝規范見表4[20−23],表格中單元名稱與圖1和圖2相對應。
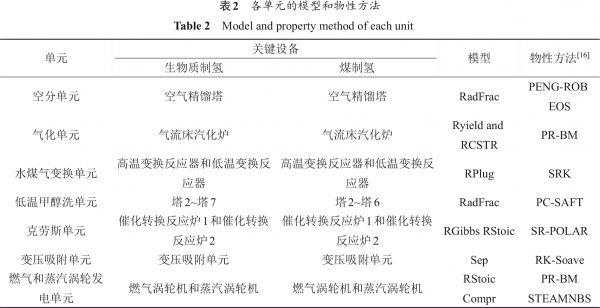
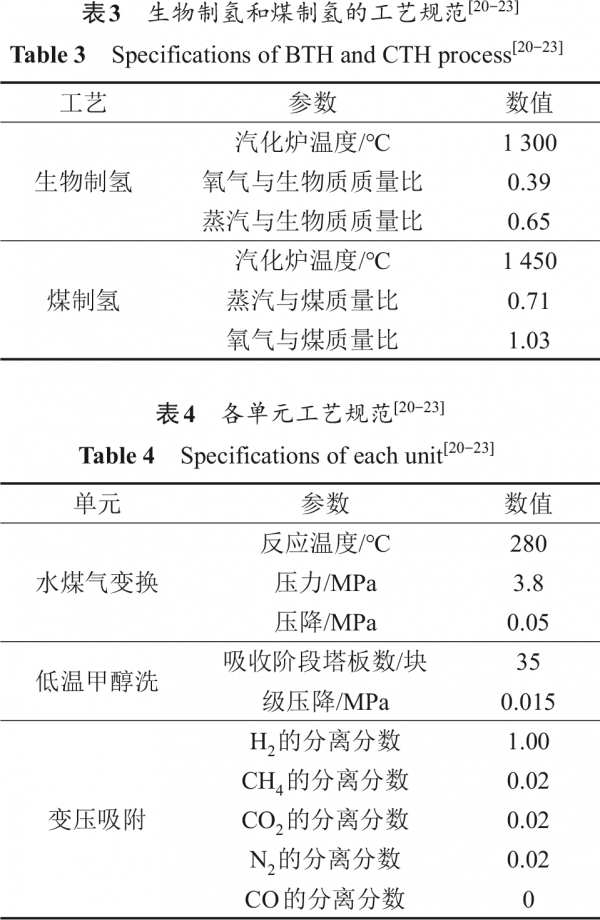
設定年制氫能力為1.8×108m³,生物質制氫工藝原料消耗量為10990kg/h,而煤制氫工藝原料消耗量為6430kg/h,這2種工藝各單元的模擬輸出如表5所示。為保證模擬結果的可靠性,將模擬得到的結果與文獻[6,17,23−25]中的實際結果進行對比驗證,發現兩者較吻合。
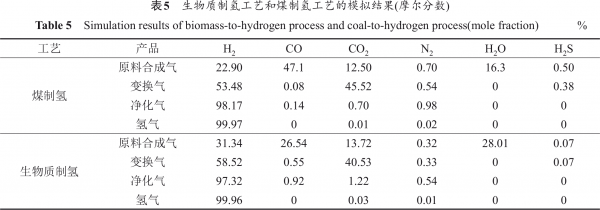
2生命周期評價
目前,生命周期評價(LCA)已被納入ISO14000環境管理系列標準,該方法已成為工藝流程設計和國際環境控制的主要評價手段。LCA的實施以國際標準(ISO14040,2006)為指導,可以對產品系統的投入、產出和潛在環境影響進行評價。LCA包括目標和范圍定義、庫存分析、影響評估和解釋4個方面。
本文主要針對制氫工藝的環境評估,通過確定制氫過程的系統邊界和功能單元,收集各階段的能耗以及溫室氣體排放情況,以計算煤制氫工藝和生物制氫工藝的能源消耗以及溫室氣體排放。
2.1系統邊界和功能單元
煤制氫和生物質制氫生產系統的生命周期邊界如圖3所示。煤制氫系統邊界主要包含3個子系統:1)煤炭開采、加工和運輸(SS1);2)煤炭預處理和氣化(SS2);3)制氫、凈化和輸運(SS3)。生物質制氫過程的邊界包含3個子系統:1)生物質秸稈的生產與運輸(SS1);2)秸稈預處理和氣化(SS2);3)制氫、凈化和輸運(SS3)。本文主要考慮子系統的碳排放、碳排放過程中的生命周期能耗以及溫室氣體排放,其中,系統邊界范圍內的主要能量輸入包括煤炭、柴油、電力等,溫室氣體主要考慮CO2,N2O和CH4的排放。

功能單元是生命周期評價中定義輸入和輸出的統一單元,其作用是為評估系統性能提供一定標準。在本研究中,將制氫過程中每小時產生的1004.5kg氫氣定義為1個功能單元。
2.2生命周期能耗
生命周期能耗由所有過程能源消耗和相應的一次化石消費因子之和決定[9,26],其計算方法見式(1)。表6所示為獲得1MJ過程能源需要消耗的化石能源。
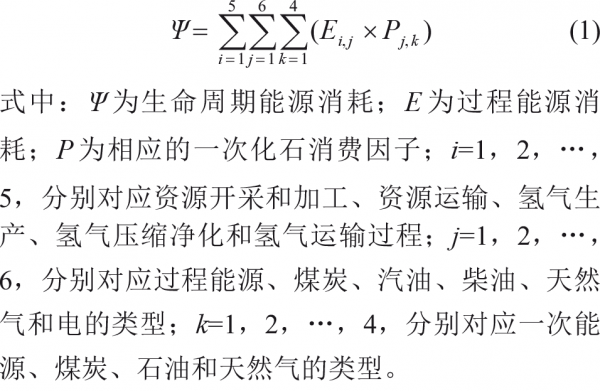
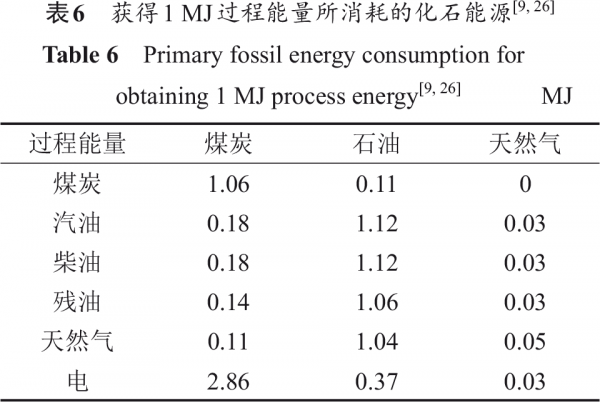
2.3生命周期溫室氣體排放
生命周期評價中溫室氣體排放考慮了CO2,N2O和CH4的直接排放與間接排放[3]。其中,直接排放的溫室氣體是指使用化石能源過程中產生的溫室氣體,而間接排放的溫室氣體則是指化石能源的生產加工以及運輸過程中排放的廢氣。結合表7[9,26],得到全生命周期溫室氣體排放的計算方法如下:
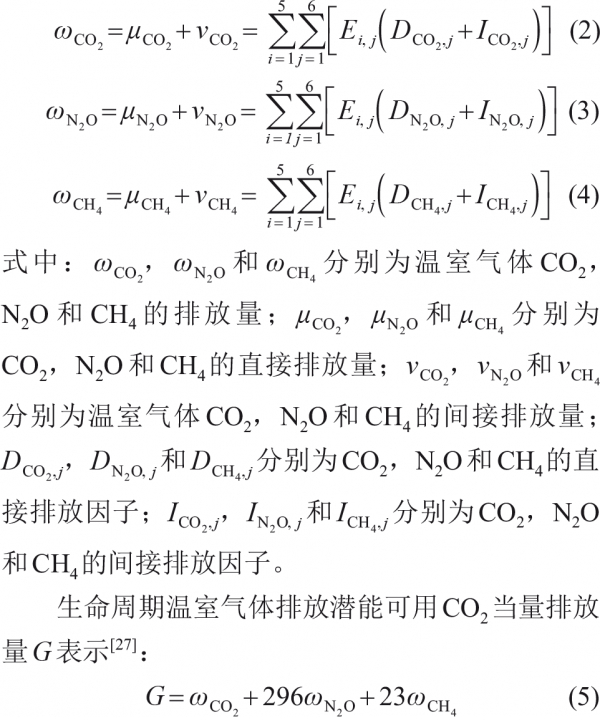
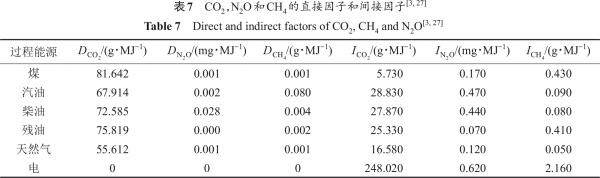
2.4生命周期清單分析
2.4.1煤制氫的過程
1)煤炭開采、加工和運輸階段。目前,中國每年煤炭生產量超過3.5億t。近10年來,約有25%的煤炭經過加工實現了清潔開采。根據文獻[28],每1MJ采煤加工過程的能源消耗如表8所示。中國煤的平均運距為600km,包括鐵路運輸500km和汽車公路運輸100km,煤炭運輸過程的驅動能源主要為柴油、汽油和電力,氫運輸距離為長途公路300km。各運輸方式的能源強度如表9所示。
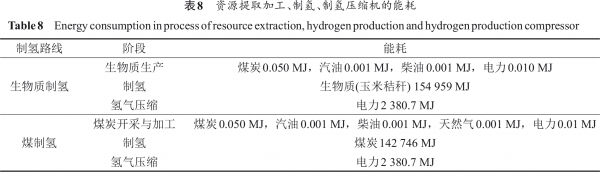
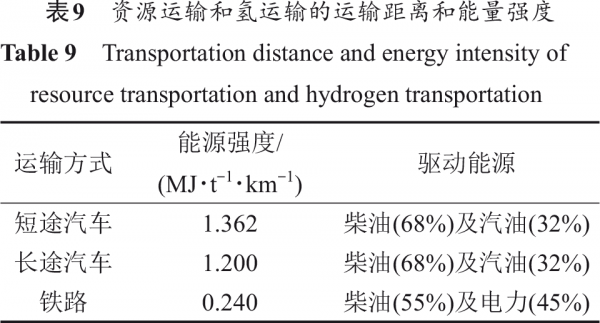
2)制氫階段。CTH-SS2中每小時可制氫1004.5kg,消耗6430kg煤炭。煤炭的低熱值為22.2MJ·kg−1,故煤制氫工藝中制氫階段的過程能耗為142746MJ。在此階段,煤炭不僅是生產氫氣的原材料,同時也用于蒸汽以及電力生產。在CTH-SS2中,溫室氣體的主要來源是生產過程中的尾氣直接排放。煙道內每小時可排放CO2尾氣13794.3kg。根據工藝原理,煙道內幾乎不存在N2O和CH4,因此,本系統不予考慮。
3)氫氣凈化及輸送階段。高純度(99.97%)氫氣主要由變壓吸附裝置生產,其生產能力為1004.5kg/h。氫壓縮過程中消耗電力1.52MW,其中,0.86MW的電力副產品氫能可用于氫壓縮機組(見表10),所以,僅需要耗電0.66MW(即2380.7MJ·h−1),如表8所示(假定公路汽車輸運氫的距離為300km)。

2.4.2生物制氫過程
1)秸稈的生產與運輸階段。中國秸稈資源十分豐富,每年的秸稈產量將近10t。根據文獻[9],每采掘加工1MJ玉米秸稈的工藝能耗如表8所示。本文中,玉米秸稈的平均傳輸距離為汽車公路運輸100km及鐵路運輸500km,與煤炭的平均傳輸距離相同,均為600km。也就是說,生物質制氫過程與煤制氫過程的驅動能量相等。
2)制氫階段。BTH-SS2中每小時可制氫氣1004.5kg,消耗10990kg生物質秸稈。而此生物質原料的低熱值為14.1MJ·kg−1,因此,能源消耗為154959MJ,見表8。從圖2可知,制氫階段中尾氣的直接排放造成了大量的溫室氣體排放,煙道內尾氣CO2每小時排放量為23576.9kg(見表10)。與煤制氫過程相同,煙道內基本不存在N2O和CH4,因此,在本分系統中不考慮。
3)氫氣凈化運輸階段。高純度(99.96%)氫氣由變壓吸附裝置生產,其質量為1004.5kg。氫壓縮過程消耗電1.52MW,額外的0.86MW電力的副產品氫可用于氫壓縮機組(表10),只有0.66MW(即2380.7MJ·h−1)電需要購買(見表8,同樣假定氫的公路傳輸距離為300km)。
3結果與討論
3.1技術經濟分析
3.1.1設備投資總額
總資本投資包括直接投資與間接投資、流動運營投資與固定資本投資[29],其中,流動運營投資用于維持日常運營,固定資本投資為工廠設備費用。這2種制氫系統所需的設備投資計算式為
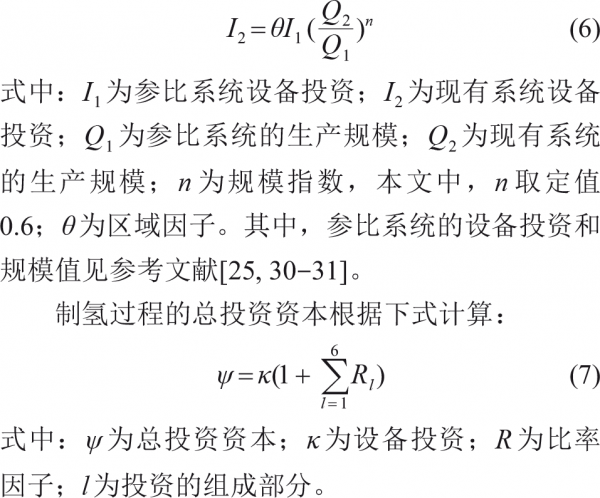
利用式(7)計算得到煤制氫過程與生物質制氫過程的總投資資本,如圖4所示。生物質制氫流程的總投資資本為1.2×109元,煤制氫流程的總投資資本為9.5×108元,兩者總投資資本具有一定可比性。對于同樣規模的氣化爐,生物質制氫工藝的投資資本約為煤制氫工藝投資資本的1.2倍。這主要是由于,一方面,生物質制氫工藝與煤制氫工藝相比原材料的消耗更大,另一方面,生物質制氫工藝中氣化爐的體積更大。所以,當生物質制氫工藝和煤制氫工藝的生產能力相同時,前者的總投資資本為后者的1.2倍。
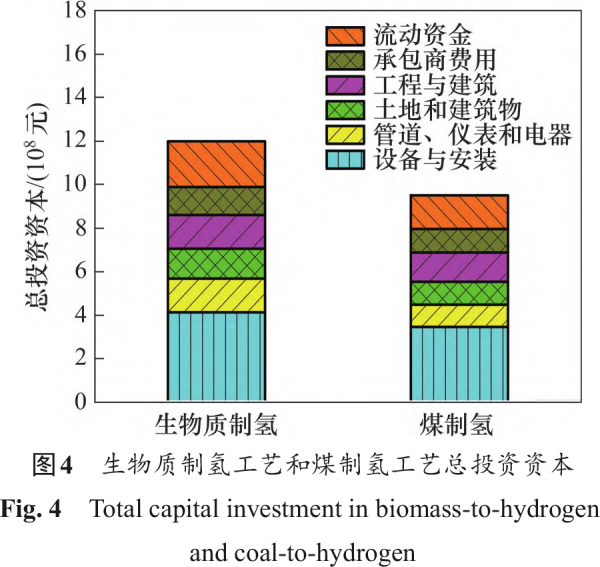
3.1.2生產成本
公用工程成本和原料成本是生產成本的主要組成部分。計算生產成本的部分假設見表11[30]。假定時間為25a,殘值為4%,采用直線法計算折舊成本。生產成本的計算式為
C=CR+CO+CU+CP+CD+CA+CS(8)
式中:CR為原材料成本;CO為運營維護成本;CU為公用事業成本;CP為工廠間接成本;CD為折舊成本;CA為管理成本;CS為銷售和分銷成本。
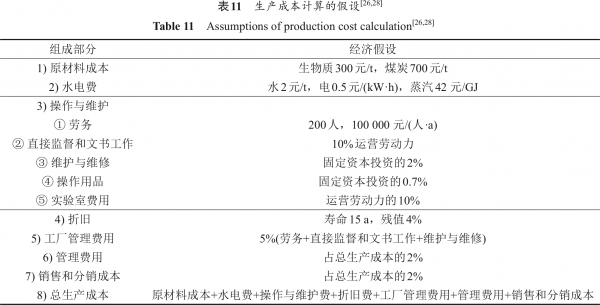
將計算得到的生產成本進行進一步分解,如圖5所示。1m³生物質制氫工藝生產成本為0.306元,而煤制氫工藝的生產成本為0.370元,前者的生產成本比后者低17.3%。從圖5可知:原材料成本、設備費和折舊費在生產成本中占比較高。在生物質制氫過程中,原材料消耗占比最大,為總生產成本的44.7%,其次是折舊和設備費,分別占20.2%和17.8%。盡管原料消耗大,但由于生物質價格低廉,因此,生物質制氫生產成本仍較低。同樣地,在煤制氫工藝中,原材料消耗占總生產成本的51.4%;其次是設備費,占總生產成本的22.0%,而折舊費所占比例為13.6%。
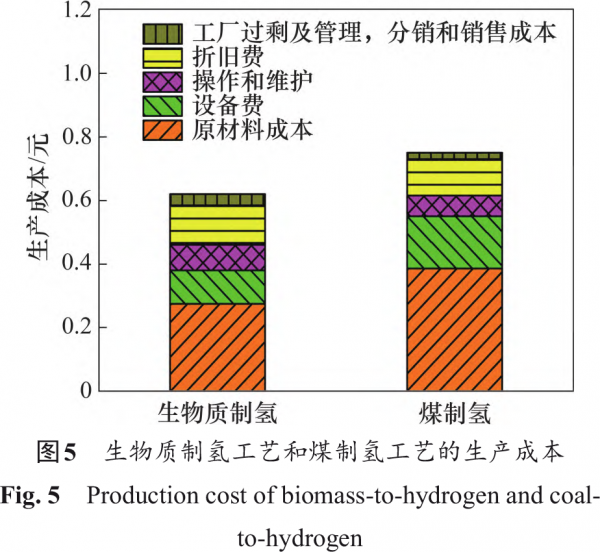
生物質制氫和煤制氫工藝的生產成本之比根據式(9)計算,結果如圖6所示。圖6中,橫坐標為煤炭價格,從200元/t到1200元/t不等。生物質價格從100元/t到800元/t不等,對生物質荷煤炭的成本進行分析。圖6中水平虛線表示生物質制氫的生產成本等于煤制氫的生產成本。在虛線以上,生物質制氫的生產成本高于煤制氫生產成率;在虛線以下,煤制氫的生產成本高于生物質制氫生產成本。
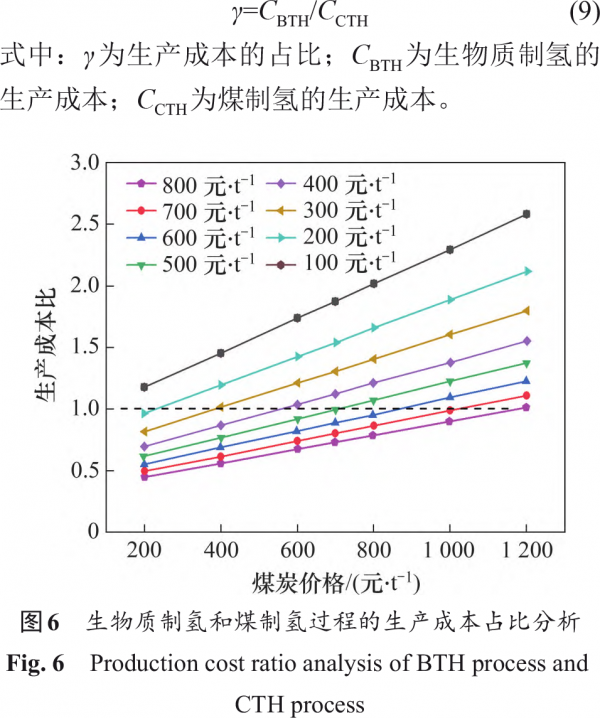
從圖6可以看出,在玉米秸稈等生物質產品價格不變的正常情況下,生產成本的占比會隨著煤炭等化石燃料產品價格的持續上漲而大幅增加。但在煤炭等化石燃料的產品價格不變的正常情況下,生產成本的占比卻隨著玉米秸稈等生物質原燃料價格的上漲而降低,這意味著生物質價格的進一步上漲減少了生物質制氫和煤制氫之間的生產成本差距。隨著原料價格的變化,生物質制氫工藝的波動小于煤制氫工藝的波動。結果表明,在較低的原料價格下,生物質制氫和煤制氫工藝的經濟性能沒有顯著差異。然而,在原材料價格較高的情況下,經濟性能會有很大的不同。因此,可以得出這樣的結論:生物質制氫過程在抗價格風險方面比煤制氫過程具有更好的性能。
3.1.3碳稅
在不同碳稅價格下,生物質和煤炭的價格如圖7所示,其中,橫坐標為生物質價格,從100元/t到400元/t不等,碳稅從0元/t到600元/t不等;縱坐標為煤炭價格,從0元/t到700元/t不等。煤制氫過程的煤炭價格隨著碳稅增加而降低。考慮到生物質在整個生命周期中的二氧化碳平衡,生物質價格不會隨著碳稅的變化而發生顯著變化,這可能是因為生物質屬于碳中性的能源,所以,生物質能源的大量使用不會向大氣中排放額外的碳,并且煤制氫工藝比生物質制氫工藝產生的溫室氣體更多,因此,在考慮碳稅的市場中,生物質制氫過程顯示出更好的性能。
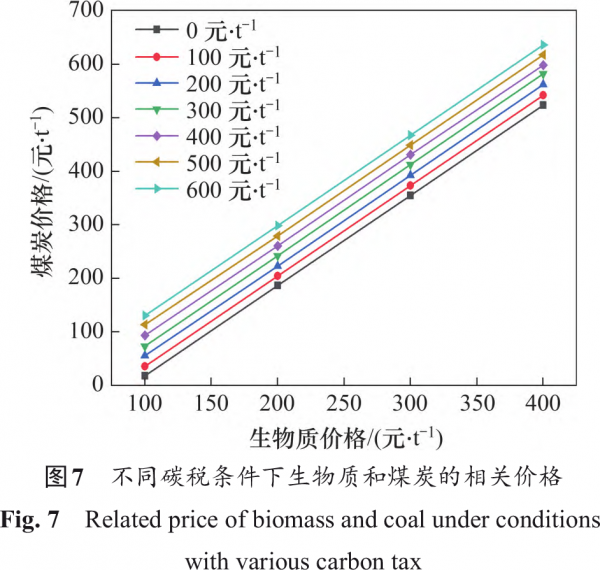
3.1.4能效分析
以年產1.8×108m³的煤制氫和生物質制氫工藝為基礎,通過模擬計算,得到原料和公用工程的消耗量。根據這些類型消耗的較低熱值,可通過下式計算過程的能量轉換效率:
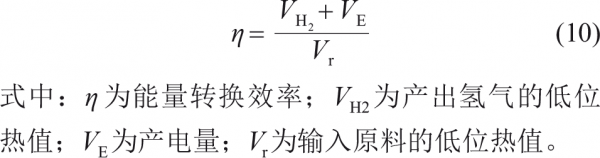
生物質制氫工藝的能量流如圖8所示。從圖8可見:空分單元(ASU)、生物質預處理裝置(BPU)、氣化單元(GU)、水煤氣變換單元(WGSU)、酸性氣體脫除單元(RU)、變壓吸附單元(PSAU)、克勞斯單元(CU)和燃氣和蒸汽渦輪機單元(GSTU)的能量效率分別為58.00%,97.37%,64.60%,90.60%,95.80%,98.80%,45.20%和88.62%。煤制氫的能量流程圖如圖9所示。從圖9可見:空分單元(ASU)、氣化單元(GU)、水煤氣變換單元(WGSU)、酸性氣體脫除單元(RU)、變壓吸附單元(PSAU)、克勞斯單元(CU)和燃氣和蒸汽渦輪機單元(GSTU)的能量效率分別為57.70%,68.90%,91.90%,96.40%,98.90%,52.20%和88.80%。
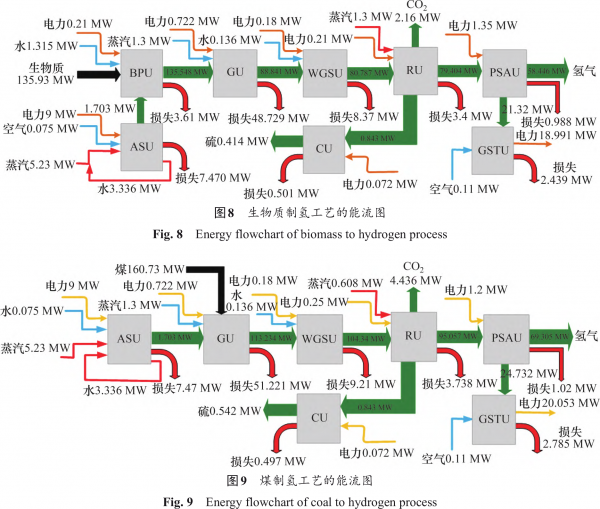
3.2生命周期評價分析
3.2.1生命周期能源消耗
根據表5、表7和表8,由式(1)計算得到煤制氫過程與生物質制氫過程的生命周期能耗。煤制氫過程每功能單元中的能源消費總量為4.78×1011J,生物質制氫過程為1.18×1011J。對煤制氫過程與生物質制氫過程不同階段的生命周期能耗進行分析,結果如圖10所示。從圖10可見:對于煤制氫工藝,其制氫能力為1004.5kg·h−1,煤炭的開采與運輸階段每生產1004.5kg氫氣的全生命周期能耗為1.83×1011J;而對于同樣的制氫能力,生物質制氫工藝中秸稈生產與運輸階段的生命周期能源消耗為5.82×1010J。故在煤制氫工藝的第一階段需要6430kg煤炭,而生物質制氫工藝的第一階段需要10990kg玉米秸稈。由于采煤與加工煤過程較復雜,消耗能量較多,而生物質(玉米秸稈)的生產與加工較簡單,不需要消耗大量能量,這使得煤制氫過程所獲原材料質量較生物質制氫過程低41.5%,而能源消耗比生物質制氫工藝高2.15倍。對于同樣的運輸距離,煤制氫過程和生物質制氫過程在資源運輸階段和輸送階段每生產1004.5kg氫氣的生命周期能耗分別為6.34×109J和1.86×109J。從圖10可以看出,在制氫階段,兩者有所不同,煤制氫過程全生命周期能耗為3.23×1010J,而生物質制氫過程則為3.07×1010J。產生這一差異的原因主要是氣化過程消耗了大量能量如蒸汽、煤炭和電力。
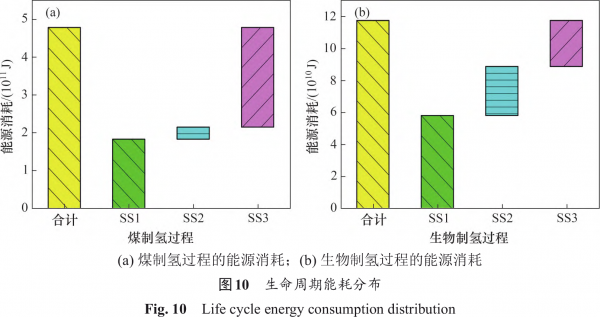
從圖6可見煤制氫工藝在氫氣凈化階段生產1004.5kg氫氣的生命周期能耗為2.63×1011J,而從圖10可知生物質制氫工藝該階段的生命周期能
耗為2.88×1010J。由于分離和凈化過程對電力、蒸汽等能量的需求較大,而這些能量主要由化石能源提供,因此,制氫過程投入階段主要為資源生產加工以及氫氣凈化和運輸(見圖6)。
3.2.2生命周期溫室氣體排放
對煤制氫過程與生物質制氫過程生命周期進行評價,根據表6~8,利用式(2)~(5)對過程中溫室氣體排放進行計算,結果如圖11所示。從圖11可見:對于1個功能單元來說,在煤制氫過程中煤炭開采和運輸階段排放的CO2溫室氣體為12.15t,而生物質制氫過程中秸稈生產和運輸階段排放的CO2溫室氣體為2.13t。對于同樣的運輸距離,兩者在資源運輸階段排放的生命周期CO2溫室氣體均為0.18t,氫氣運輸階段排放的CO2溫室氣體均為0.066t。

在制氫階段,煤制氫過程與生物質制氫過程產生的全生命周期CO2溫室氣體排放為31.57t和1.71t。在氫氣凈化階段,煤制氫過程產生的CO2溫室氣體排放為8.37t,而生物質制氫過程為1.57t。結合前面生命周期能耗分析可知,由于此階段中氫氣分離和純化過程需要消耗大量化石能源,會導致潛在的溫室氣體排放。從圖11可以看出,全生命周期溫室氣體排放主要來源于資源加工、生產運輸和制氫階段。
4結論
1)從總投資、生產成本等方面進行了績效比較分析,生物質制氫法的總成本低于煤制氫法的總成本。隨著生物質價格的進一步提高,生物質制氫和煤制氫的生產成本差距將加大。
2)生物質制氫過程的溫室氣體排放量相比煤制氫過程的排放量較低,而煤制氫過程的生命周期能耗相比生物質制氫過程的生命周期能耗高2.15倍。對比煤制氫和生物質制氫過程在生命周期中的能耗和溫室氣體排放結果,生物質制氫過程對于實現清潔生產和解決能源危機具有重要的指導意義。
3)總體來說,生物質制氫過程將在未來能源系統發展中發揮重大作用,對生物制氫和煤制氫這2種工藝進行技術經濟分析和評價對提高能源利用率、改善能源結構、促進國民經濟可持續發展具有重要的戰略意義。
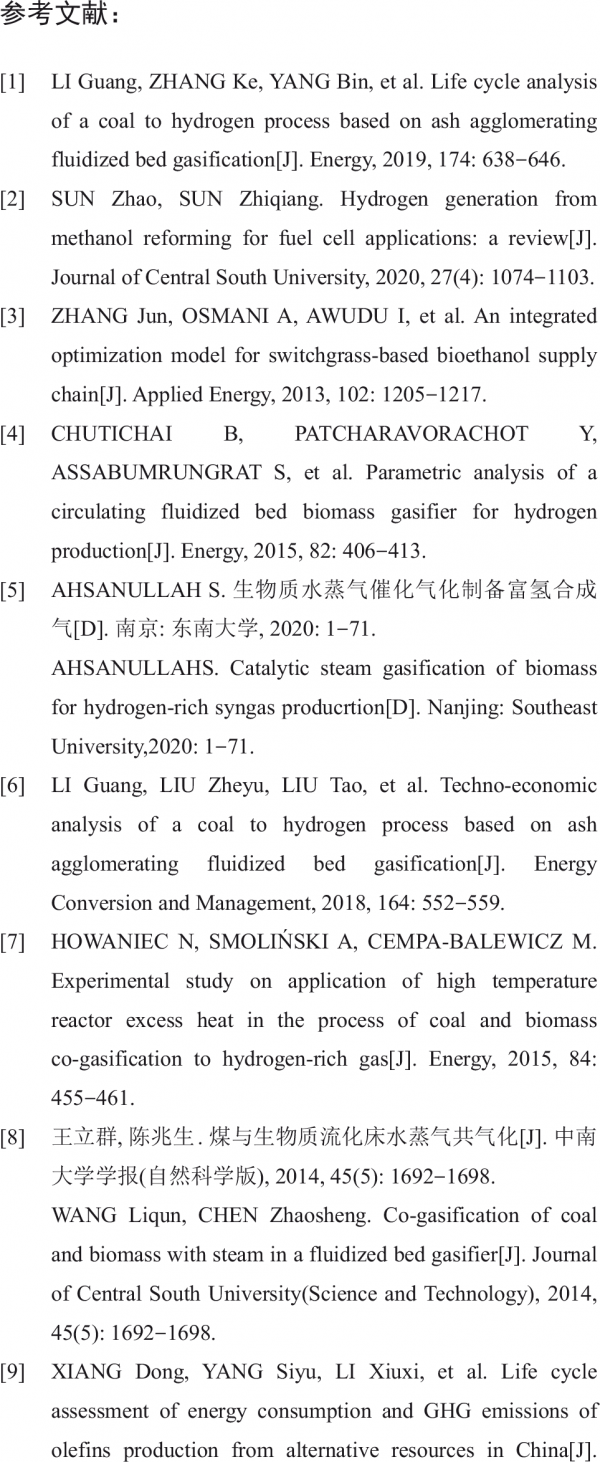
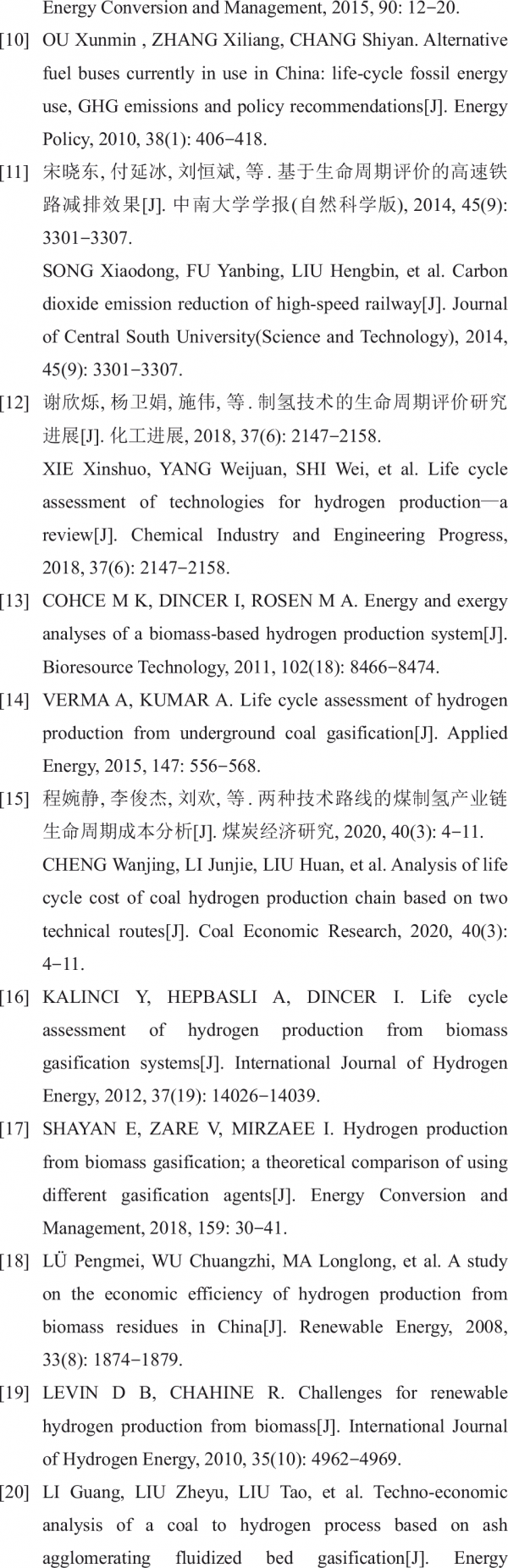
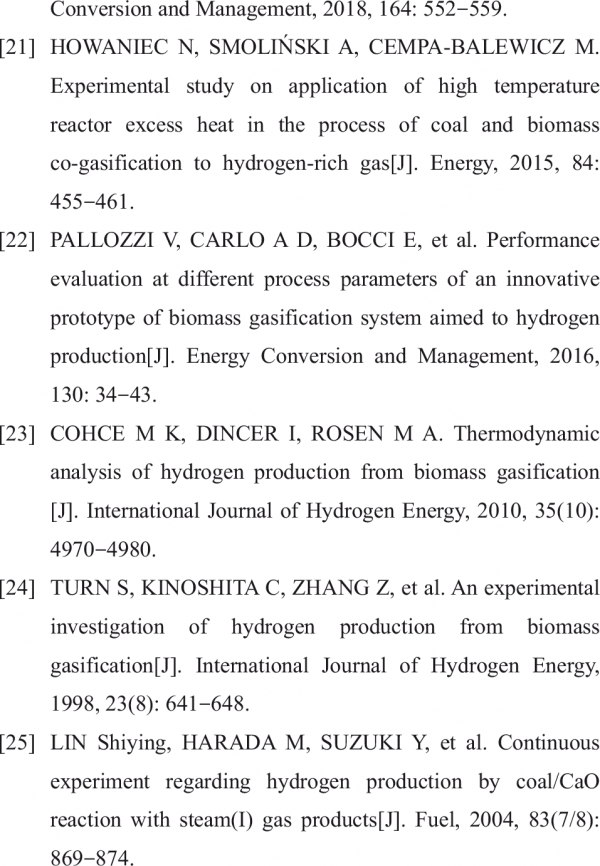
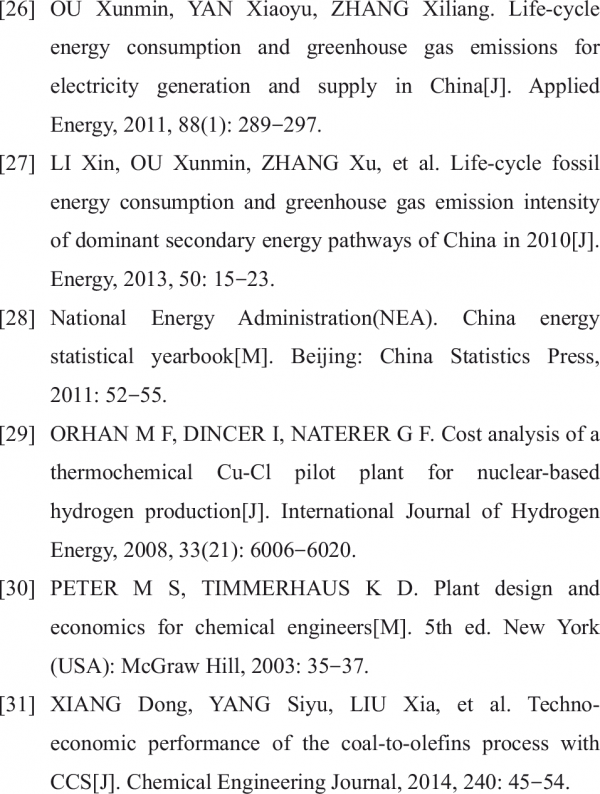 |