彭源德,鄭科,楊喜愛,嚴理,唐守偉,朱愛國,熊和平
(中國農業科學院麻類研究所,長沙410205)
摘要:在微生物預處理苧麻韌皮的基礎上,進行了pH值、酶用量、葡萄糖濃度和原料處理方式等對苧麻纖維質酶降解的單因子試驗和正交試驗。結果表明,苧麻纖維質酶解的起始pH值為5.0左右,總糖轉化率最高,達72.361%;在一定的酶濃度范圍內,隨著酶量的增加,苧麻纖維質的總糖轉化率提高,酶的適宜用量為:木聚糖酶5%、纖維素酶10%;水解液中葡萄糖濃度在0.5%以下時,苧麻纖維質的總糖轉化率不受影響,葡萄糖濃度在0.5%以上時,隨著水解液中葡萄糖含量的增加,總糖轉化率下降;苧麻纖維質酶解過程中,對原料進行機械處理,有利于提高酶的水解效率;苧麻纖維質酶解的最適條件為:pH值4.5~5.5、纖維素酶濃度8%~11%、葡萄糖濃度小于0.5%、原料不洗直接進行剪碎處理。
0引言
隨著化石燃料等不可再生資源的逐步消耗殆盡,開發利用可替代能源為當務之急。近年來,國內外學者廣泛開展了植物纖維質如玉米秸稈、甘蔗渣、檸檬酸渣、酒糟、稻殼等通過生物轉化得到燃料乙醇的研究。以植物纖維質原料生產乙醇的關鍵環節之一是將纖維素和半纖維素水解為單糖,即糖化過程,而酶糖化技術是被普遍看好的糖化工藝。例如,加拿大的Iogen公司,利用從遺傳工程真菌所制成的纖維素酶有效地使纖維素水解為葡萄糖和其它糖類。Zomed等(1991)利用純化的β-葡萄糖苷酶和纖維素酶同時酶化纖維素,大大提高了糖化速率;Hari等(2000)利用模式菌種里氏木霉(Trichoderma reesei)QM-9414產生的纖維素酶對香蕉葉子進行降解,獲得了較高的糖化率。國內,木質纖維素等生物酶降解生產燃料乙醇的研究剛剛起步。
張發群等(1991)糖化蔗髓時,先用CaO處理,再Trichoderma Uoningji P2菌株所產生的酶液進行分解,得糖率為45.3%~54.5%,全纖維素轉化率平均為73.8%;沈金龍等(2004)利用纖維素酶高產菌株里氏木霉突變株813A所產生的纖維素酶,對天然木質纖維素的水解糖化過程進行了研究,玉米葉和楊樹葉的水解糖化率分別達到86.12%和56.10%,酒精轉化率79.14%~72.11%。但由于受硫酸預處理的環境污染嚴重,酶的活力不高,技術不完善等因素的影響,導致纖維質生產燃料乙醇的產業化進程緩慢。作者采用微生物預處理和酶降解糖化技術,將苧麻纖維質酶降解生產燃料乙醇取得重要進展。前文報道了外界因子對纖維質酶降解的影響。
本研究擬在此基礎上,通過研究起始pH值、酶和葡萄糖濃度及原料物理處理方式等主要因素對苧麻纖維質酶降解的影響,優化酶降解的條件,確定苧麻纖維質酶解糖化的工藝流程和技術參數,為加速研究苧麻木質纖維素生產燃料酒精酶糖化技術,改良酶促反應條件(如除去某些酶解產物、降低酶促反應平衡點)研究等方面提供科學依據,進而充分挖掘中國特有的苧麻纖維質資源,緩解能源緊張的矛盾,達到保護生態環境的目的。
1材料與方法
1.1材料
1)預處理菌株
由中國農業科學院麻類加工與環保研究室選育并保藏的麻類脫膠高效菌株。
2)纖維素酶和木聚糖酶
由湖南尤特爾生化有限公司提供的液體纖維素酶和木聚糖酶,其活性分別為2000IU/mL和6000IU/mL左右。
3)主要儀器與設備
分析天平、精密pH計、磁力加熱攪拌器、分光光度計、搖瓶機、生化培養箱、高速組織搗碎機、電熱恒溫水浴鍋、計時器、移液器和微量進樣器等。
4)化學試劑
試驗涉及的主要化學試劑有:CMC(sigmac-5678)、木聚糖、聚半乳糖醛酸、無水葡萄糖、檸檬酸—磷酸氫二鈉緩沖溶液、氫氧化鈉溶液、鹽酸、硫酸、3,5-二硝基水揚酸、酒石酸鉀鈉、高錳酸鉀和草酸鈉等,工藝輔料主要包括菌種活化、擴大培養和發酵的培養基組分等,這些物質均為市售商品。
1.2方法
1)預處理
用Ym68'菌株對苧麻韌皮進行預處理,即利用微生物酶催化,分、降解生苧麻中的非纖維素物質。準確稱取苧麻韌皮10.0000g,按20%(對苧麻韌皮)的接種量,將培養5~6h的高效菌株Ym68'接種到生苧麻上;在35℃左右條件下,靜置濕潤發酵6~8h,洗凈備用。
2)單因子試驗
采用500mL錐形瓶盛微生物預處理后的苧麻纖維質10g左右,混合酶水解時,木聚糖酶用量5%、纖維素酶用量10%(以酶液對苧麻纖維的質量%表示),浴比1∶10,pH值5.5,置50℃恒溫處理5h;纖維素酶水解時,酶用量為10%(以酶液對苧麻纖維的質量%表示),浴比1∶15,pH值4.5,置50℃恒溫處理6h;3次重復,測定處理前、后液體中的還原糖量。
根據研究目的,設置pH值、溫度、原料處理方式、葡萄糖濃度等對苧麻纖維質酶降解糖化的影響試驗。
1)纖維質糖化的起始pH值試驗:分別設置pH值為4.5、5.0、5.5、6.0、6.5和7.0,進行苧麻纖維質的混合酶(纖維素酶和木聚糖酶)和纖維素酶的水解糖化,測定水解液前后的還原糖量。
2)酶的用量試驗:木聚糖酶用量分別為2%、5%和8%,纖維素酶量分別為5%、10%和15%;單一纖維素酶用量均為10%,進行苧麻纖維質的混合酶(纖維素酶和木聚糖酶)和纖維素酶的水解糖化,測定水解液前后的還原糖量。
3)葡萄糖濃度試驗:在苧麻纖維質水解糖化時,分別加入0.5%、2%、5%和8%的葡萄糖、以未添加葡萄糖的為對照,測定起始和終點的還原糖量。
4)原料處理方式:設置微生物預處理后的苧麻纖維質直接酶水解、剪碎成0.5cm、搗碎和風干剪碎等四種處理方式,進行苧麻纖維酶水解糖化。
3)正交試驗
在苧麻纖維質酶水解糖化過程中,對起始pH值、酶和葡萄糖濃度及原料物理處理方式等4個因素,進行3個水平的正交試驗。以確定影響苧麻纖維質酶水解糖化的最大因素,找出最佳工藝條件。正交設計表中水平與因子L9(3^4)各因素的取值范圍見表1,按L9(3^4)安排的試驗計劃見表2。
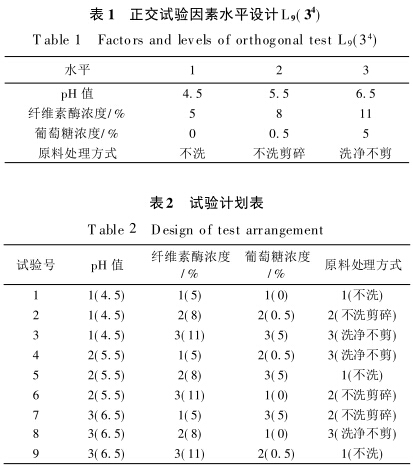
4)測定方法
還原糖的測定采用DNS比色定糖法(540nm);pH值用PHS-3C型酸度計測定;酸性纖維素酶活性測定采用CMC法;木聚糖酶的酶活測定采用DNS法,底物為sigma公司生產的木聚糖。
2結果與分析
2.1起始pH值對纖維質水解糖化的影響
pH值對纖維質水解糖化的影響結果列于表3,從表3可以看出,pH值在4.5~6.5之間時,苧麻纖維質的糖化率沒有極顯著差異,以pH值5.0的糖化率最高,酶活性最大;在pH7.0時,糖化率極顯著降低。因此,可以得出,5.0是苧麻纖維質酶水解糖化的最適pH值,總糖轉化率為72.361%。
2.2酶濃度的影響
由表4可以看出,在一定酶濃度范圍內,隨著酶量的增加,酶的水解效率提高。木聚糖酶由2%增加到5%、纖維素酶從5%提高到10%,糖化率提高近9個百分點,有極顯著差異;但木聚糖酶和纖維素酶的酶量再分別增加到8%和15%時,糖轉化率幾乎沒有差異。這是由于在一定條件下,一定量的半纖維素和纖維素分子能和酶分子結合的結合點數有限,當這些結合點全被酶分子占據后,酶分子處于飽和態,再增加酶用量,也起不到酶解作用。因此,從經濟角度考慮,酶用量以木聚糖酶5%和纖維素酶10%比較適宜。
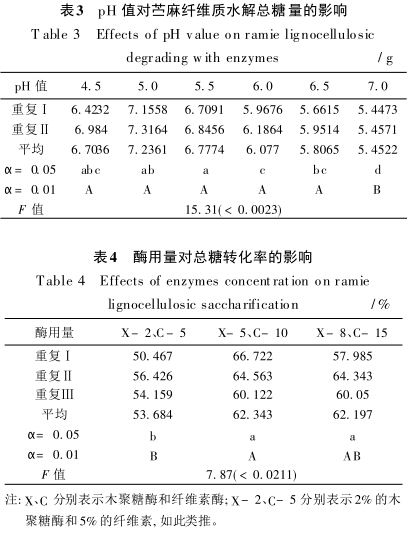
2.3葡萄糖濃度的影響
葡萄糖含量對纖維素降解的影響如表5所示,水解液中葡萄糖濃度在0.5%以下時,苧麻纖維質的總糖轉化率不受影響;葡萄糖濃度在0.5%以上時,隨著水解液中葡萄糖含量的增加,總糖轉化率下降;當葡萄糖濃度為8%,總糖轉化率下降了64%左右。
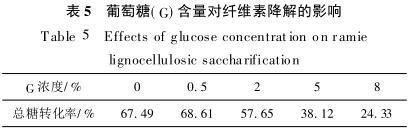
2.4原料處理方式
苧麻纖維質不同處理方式的酶水解糖化效果列于表6,表6結果表明,生物脫膠后的苧麻纖維質處理方式對酶水解糖化有明顯的影響,機械處理可加速纖維質酶水解糖化進程,糖化率提高。以搗碎處理的糖化率最高,達72.622%;其次是剪碎處理的;再次為濕潤纖維質直接水解糖化的,糖化率為62.066%;風干剪碎處理的糖化率最低,僅為32.003%。這可能是由于酶吸附于纖維素表面是纖維素發生水解的必需條件,機械處理使纖維素的比表面積增加,有利于纖維素酶的吸附,進而提高酶的水解效率。
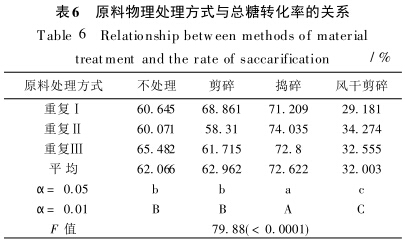
2.5正交試驗
從pH值、纖維素酶和葡萄糖濃度及原料處理方式等因素的正交試驗結果表7可以看出,4種因素對苧麻纖維質酶降解的糖化率均有影響,以葡萄糖濃度的極差最大,為16.54%;其次是原料處理方式,為12.28%;再次為起始pH值,極差8.61%;纖維素酶濃度的極差最小,僅為8.59%。也就是說,苧麻纖維質酶降解中的葡萄糖濃度對總糖轉化率的影響最大,原料處理方式次之,纖維素酶濃度的影響最小。從表7還可以看出,正交試驗中,各因子對苧麻纖維質酶降解的糖化影響效果與單因子試驗的基本一致,其酶降解的適宜條件為:pH值4.5~5.5、纖維素酶濃度8%~11%、葡萄糖濃度小于0.5%、原料進行不洗剪碎處理。
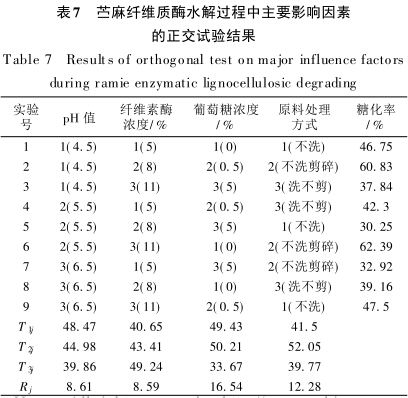
3結論與討論
在微生物預處理苧麻韌皮的基礎上,在實驗室條件下進行pH值、酶用量、葡萄糖濃度和原料處理方式等對苧麻纖維質酶降解的單因子試驗和正交試驗,可以得出如下結論:1)苧麻纖維質酶解的起始pH值為5.0左右,總糖轉化率最高,達72.361%。2)在一定酶濃度范圍內,隨著酶量的增加,苧麻纖維質的總糖轉化率提高,酶的適宜用量為:木聚糖酶5%、纖維素酶10%。3)水解液中葡萄糖濃度在0.5%以下時,苧麻纖維質的總糖轉化率不受影響;葡萄糖濃度在0.5%以上時,隨著水解液中葡萄糖含量的增加,總糖轉化率下降。4)苧麻纖維質酶解過程中,對原料進行機械處理,有利于提高酶的水解效率。5)苧麻纖維質酶解的最適條件為:pH值4.5~5.5、纖維素酶濃度8%~11%、葡萄糖濃度小于0.5%、原料不洗直接進行剪碎處理。
苧麻具有生物學產量和纖維素含量高、木質素含量低等特點,是生產燃料乙醇的理想原料之一。本文通過高效清潔的預處理(6~8h完成生物發酵)和適宜的酶促反應條件研究,獲得了較高的糖化率(72%),為苧麻纖維質酶降解生產燃料乙醇技術提供了依據。同時,根據本研究中纖維素酶和木聚糖酶的用量,估算出每噸燃料乙醇所需酶的成本在2000元左右。這與前人研究的酶解成本約占總純生產成本的40%~55%結論基本一致。通過提高酶的活性,減少酶的用量;優化酶解條件,提高酶的效率是降低苧麻纖維質酶降解生產燃料乙醇成本的關鍵。 |